Brewers around the world are in a constant battle for people’s attention, whether their products end up on shelves, in coolers, or anywhere else that potential buyers may see their products. In a constant battle for attention, you may want to give your
beer labels an extra edge to create a certain brand identity and attract consumers. However, that extra
something in your design may be an issue when it comes to label approval.
Whether you’re trying to push some boundaries or simply be clever, your beer label design is ultimately judged by government. The Alcohol and Tobacco Tax and Trade Bureau (TTB) has certain standards for what’s permissible on beer labels. As you may expect, there are a lot of practices that are prohibited for beer label design. The Code of Federal Regulations provides a very long, detailed list, so we’ll try and break down just what may land your design in hot water as succinctly as possible.
What Can’t You Put on a Beer Label?
When you’re trying to push the boundaries with your beer label, it’s important to make sure your design doesn’t conflict with any of the types of statements listed by the TTB. It’s important to note that “statements” applies to more than just text. Anything written, printed, graphic, or portrayed by some other means on a beer label, carton, or case is considered a statement of some sort. As such, any of the following types of statements can lead to the TTB denying your label design.
Untrue or misleading statements
Simply put, the TTB is going to turn you down if they think you’re lying on your label. The TTB considers a statement as untrue if it’s directly false, false by omission, generally ambiguous, or somehow misleading.
For example, a brewery positioning itself to be a microbrewery without meeting the legal definition of one can have its label denied for misleading consumers. Meanwhile, Kona Brewing Company was sued in California for misleading people to think that its beer was brewed in Hawaii. While Kona does use Hawaiian imagery and names, every label clearly states that the beer is not brewed on the island. Because of these statements, the TTB not find the labels misleading (although Kona did eventually agree to a settlement for the lawsuit).
Disparaging statements
While you may want to make a few snide comments about your competitors or some other person or entity, the TTB won’t let you make any statements they determine to be disparaging or hurtful. With that in mind, you may want to rename your batch of “At Least It’s Better Than [Blank] Schwarzbier.”
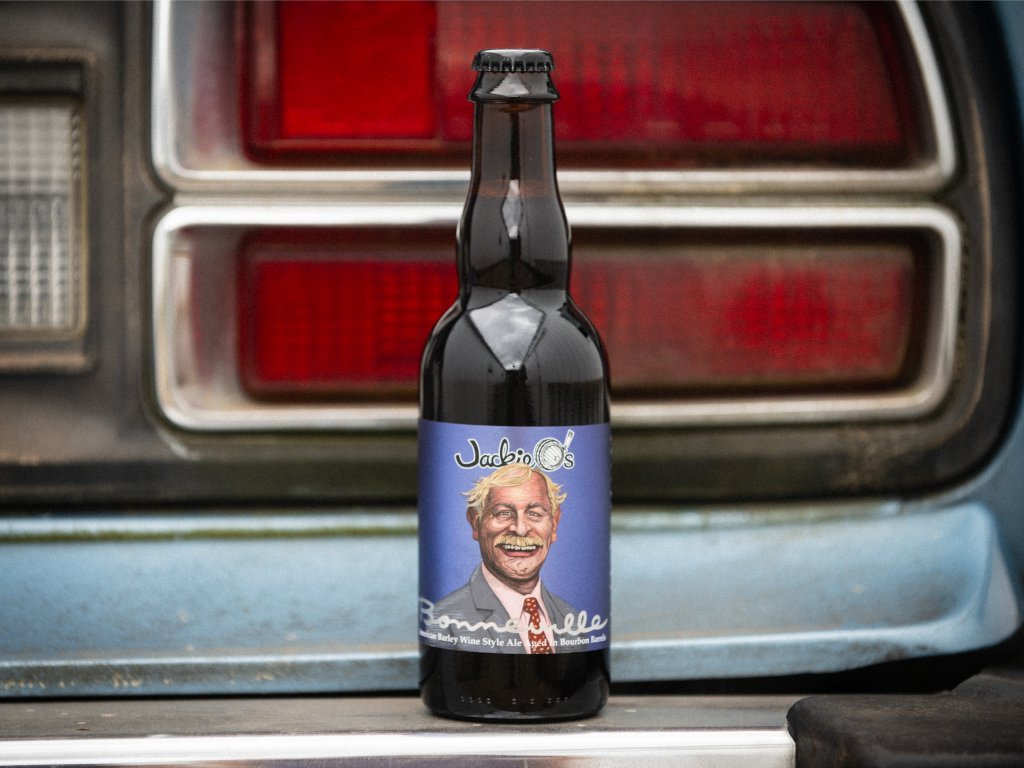
Obscenity or indecency
This section will likely be the biggest hurdle for any brewer trying to test some boundaries. According to the TTB, “any statement, design, device, or representation which is obscene or indecent” is prohibited. However, it’s not always clear what the TTB will consider off limits. This type of ruling is one of the hardest to judge because it depends on what a TTB representative finds obscene or indecent, not you or your customers.
Part of the issue with this type of prohibited statement is that various boards around the country have been inconsistent in past ruling. For example, The Alabama Alcoholic Beverage Control Board banned Founders Brewing Company’s Dirty Bastard Scotch Ale despite having already allowed the sale of Stone Brewing’s Arrogant Bastard Ale (the board eventually reversed its stance on Dirty Bastard after public outcry). As such, rulings on obscenity or indecency are up in the air, so be prepared to change your design or fight against the decision if your label might be construed as offensive in some way.
Improper guarantees or tests
Fortunately, guarantees are easier to identify than obscenity. Any element that provides some form of guarantee – aside from a money-back guarantee – is subject to denial if a TTB official finds that the guarantee may deceive consumers. The TTB will also deny any usage of analyses, standards, or tests that may mislead potential buyers. That means you can’t make a guarantee that your beer will provide short-term happiness, even if you did survey a small test group of patrons.
Names and likenesses
While you may have a great pun based on a celebrity’s names, that play on words can lead to a swift label denial (and potentially a cease and desist letter). The TTB bars the use of any names or likenesses of any prominent living individual or organization, which includes using any simulation or abbreviation to hint at the person or group. This practice is in place to prevent breweries from suggesting that certain people or organizations endorse a product.
For example, Hysteria Brewing Company in Maryland recently ran afoul of this section after using Baltimore Ravens quarterback Lamar Jackson’s likeness on a label after Jackson was named NFL MVP.
However, the TTB does provide some exceptions to this rule. Beer labels may use a person or organization’s name or likeness on a label if:
- The individual or organization is engaged in the production of the beer (such as Rogue Ale’s Beard Beer).
- A person of a trade or a brand name used the name of any living individual of public prominence, or existing private or public organization, in interest prior to Aug. 29, 1935.
Pretending to be a spirit instead of beer
Depending on your beer, you may want to utilize certain aspects of spirits on your beer label. However, it’s important not to make it seem like your beer is or contains a distilled spirit. Any statement or design element that suggests otherwise can lead to a label denial if the label does not make it clear that the beer is in fact just a beer. For example, a label that truthfully states that the beer was brewed in bourbon barrels is fine, but one that doesn’t contain any references to the product as a beer would is deemed as misleading.
Governmental connections and American insignias
You may want to show off that your beer is proud the be an American, but certain imagery or statements will lead to a quick denial by big brother. These infractions can come in a few forms:
- The use of the American flag and any flags, seals, coats of arms, crests, and other insignia associated with the armed forces of the U.S.
- The use of the word “bonded” and other variants that may imply governmental supervision over the production of the beer
- The simulation or and other design made to resemble stamps for the U.S. or foreign governments
Health-related statements
It may seem funny to make a joke that a beer a day could keep the doctor away, but doing so on a label is a quick way toward having the TTB or some other board turn down your design. Using a health claim on a label is notoriously tricky regardless of product, so it’s best to avoid making any such statements if you’re hoping for label approval, even if that claim is made as a joke.
Shows of strength
Imagine that you brewed a lovely dark beer that clocks in at a relatively hefty ABV. You may want to present to potency of your porter by calling it “strong” on the label. Unfortunately, the TTB isn’t a fan of such language. Any words along the lines of “strong,” “high test,” “high proof,” or other statements that infer alcoholic strength is off limits on beer label unless such language is required by your state’s laws.
Numerals are also a potential pain point. While alcohol by volume statements may use digits, you can’t use numerals elsewhere on your label if it can be considered as a statement of alcoholic content.
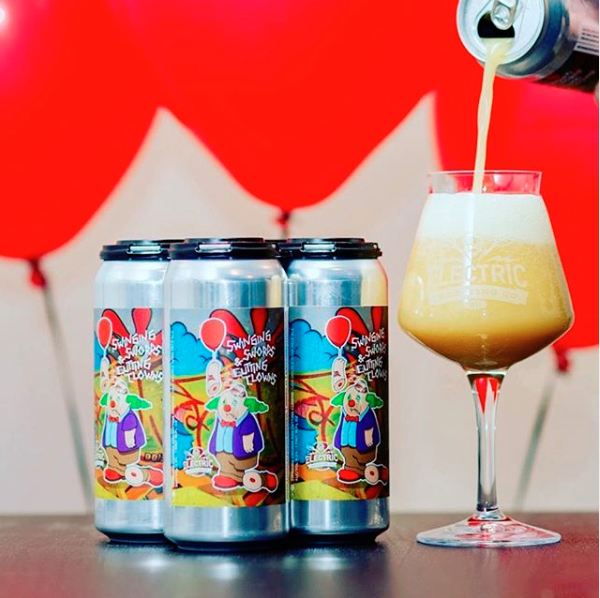
What Happens if the TTB Denies Your Beer Label Design?
Let’s pretend that you came up with a great label design and submitted a Certificate of Label Approval (COLA) to the TTB, but the organization rejected your label. Not only is a rejection frustrating, it can also delay your plans since the TTB can take up to 90 days to process a label application. Some reasons for rejection will be easier to fix, such as removing untruthful statements or disallowed imagery. However, more subjective grounds for rejection like what is considered obscene is tricky.
If the TTB denies your application, you’ll either want to modify your design based on the group’s feedback or fight the ruling. One of the most prominent examples of such a fight was when the Michigan Liquor Control Commission found the name and label of Flying Dog Brewery’s Raging Bitch Belgian-Style IPA to be offensive. Flying Dog fought the ruling in various courts until the brewery came out victorious – in 2015 after a six-year battle.
Fortunately for Flying Dog, they had the means and determination to take that fight to court, but you may not want – or be able – to do the same. In that case, it’s better to regroup and think of an alternate solution. For example, Lagunitas Brewing Company made a beer called “The Kronik” that was initially approved in the state of California, but rejected when Lagunitas resubmitted the design in order to sell the beer in multiple states. Fed up with the agency’s inconsistency involving, Lagunitas renamed the beer “Censored” in protest.
Unfortunately, there isn’t always an exact answer as to what will or won’t be approved by the TTB. If you think there may be an issue, it’s always a good practice to hope for the best but prepare for the worst.
My Label Got Approved – What Now?
First off, congratulations! Now that the TTB has signed off on your new label design, it’s time to make sure the finished product does your design justice. At Blue Label, we have the expertise and technology to provide the perfect labels for your beer cans or bottles. We’ll work with you on everything from identifying the right material for your performance needs to providing special printing capabilities that will highlight your design.
Ready to showcase your new beer label design? Contact us today to have us print quality beer labels for your brewery.